Where next for the poultry industry? The sector has made significant steps forward over the last few decades in response to margins continually getting squeezed and consumer expectation increasing. But, it’s time to make further advancements.
Where next for the poultry industry? The sector has made significant steps forward over the last few decades in response to margins continually getting squeezed and consumer expectation increasing. But, it’s time to make further advancements.
As an industry we’re already collecting and monitoring data that allows us to benchmark performance. However, in many cases this relies on producers manually inputting data on a regular basis, which is where the industry is currently falling short.
However, the solution to this current challenge is not far away. A remote monitoring system that can be set-up on farms to capture accurate, real-time data on numerous key environmental and health parameters will soon be commercially available. This data will be collated in a bespoke analytics platform ready for interpretation by producers, vets and other key stakeholders in order to inform on-farm decisions.
For producers, this will offer many benefits:
- Eliminate the requirement to manually enter data which will help overcome issues with inaccuracy and inconsistency
- Less labour intensive
- Provide producers access to reliable, real-time data remotely
Over the last six months we’ve been trialling this technology on broiler farms, and have specifically looked at how the implementation of sensors in poultry houses has helped identify variations that could affect bird health, welfare and performance.
Trial results – broiler farm case study
On one specific farm, forty wireless sensors were installed in one poultry house across multiple internal ‘zones’, the results of which are detailed below.
At chick placement, the sensors highlighted that the poultry house was 1.50C too cold (see graph one). At day seven, the sensors highlighted a high degree of temperature variation throughout the house with some areas above the optimum temperature and some below (see graph two).

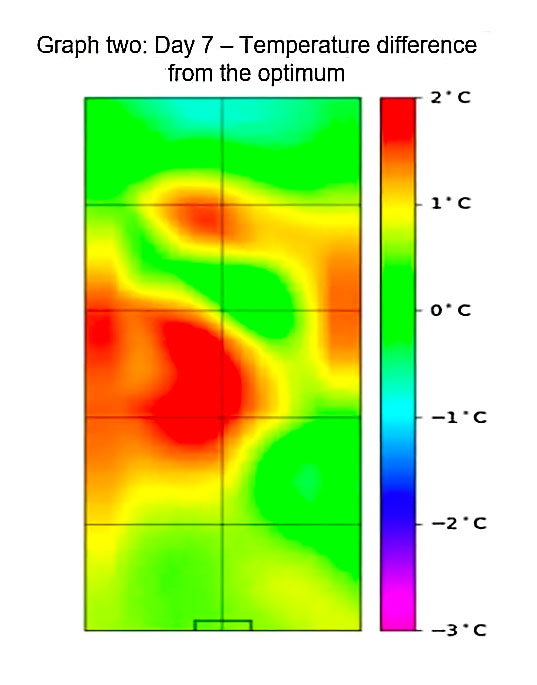
Because the house temperatures were too cool when the chicks arrived, it was more challenging to achieve a profitable FCR (Feed Conversion Ratio) and EPEF (European Production Efficiency Factor). In this specific example, the birds finished approximately three days behind the target weight.
Without this real-time monitoring system in place, we wouldn’t have been able to pinpoint as accurately why these birds did not reach their full potential and make adjustments to allow future crops to thrive.
Graph three and four showcase temperature variation throughout a crop with graph four highlighting how data from previous crops allowed the producer to implement changes that saw the bandwidth of temperature variance tighten.
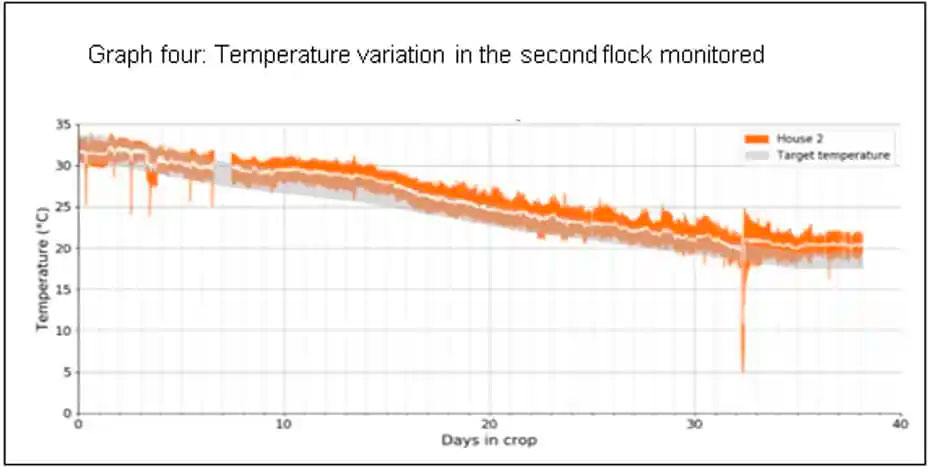
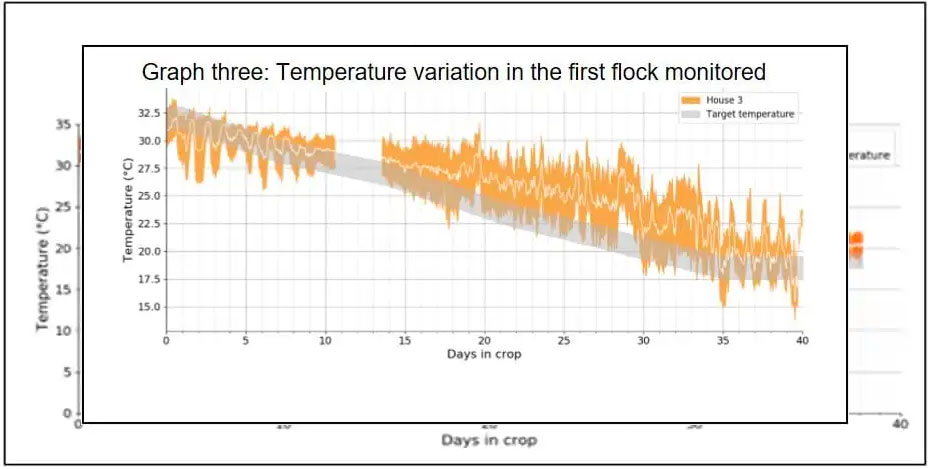
In this instance the producer changed the set-up of the climate control system to ensure it was triggered sooner when conditions in the house varied from set targets. They’ve also taken to not adding shavings to houses until all of the floor area has reached the optimum temperature for chick placement.
Making changes to ensure optimum temperatures are achieved throughout the whole poultry shed, at key milestones within a broiler birds life cycle, has led to performance improvements between the two crops of 13 FCR points and 65 EPEF points. This equated to an improvement of 24p/m2/week, which, had we not had this live data, these significant results may not have been seen.
If you’re interested in finding out more about this remote monitoring system please contact the SenseHub™ Poultry Team on info@sensehubpoultry.com or +44 (0)3303 204652.